Digital Twin for Oil & Gas
Unify Operations. Maximize Uptime. Reduce Risk.
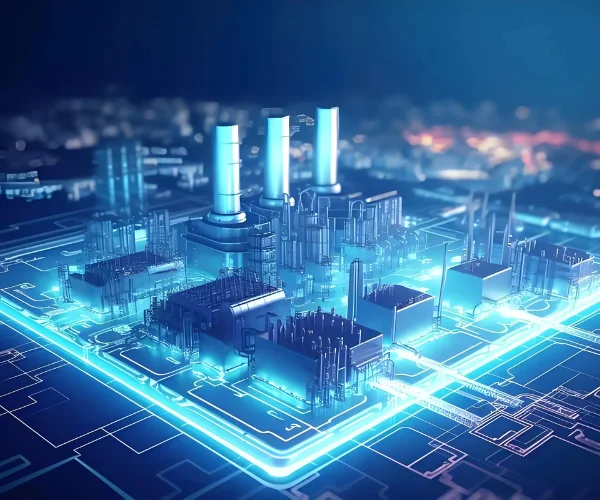
From upstream exploration to downstream refining, the oil and gas industry operates in high-risk, high-stakes environments. Operational complexity, aging assets, and safety concerns demand real-time awareness and predictive control. Our Digital Twin solution empowers oil and gas companies with the intelligence they need to operate smarter, safer, and more profitably.
Industry Pain Points

Limited Visibility Across Dispersed Assets
Oil and gas assets are spread across remote, offshore, and hazardous locations. Traditional SCADA or DCS systems offer limited visualization and contextual understanding.
Solution
Interactive 3D Digital Twin
Our Digital Twin platform offers a unified 3D view of your entire operation — from platforms and pipelines to refineries and storage tanks. Operators can remotely monitor, inspect, and analyze asset conditions with real-time sensor data layered on top of 3D models.

Unplanned Downtime and Maintenance Delays
Unexpected equipment failures lead to production loss, safety risks, and costly shutdowns — especially in offshore and midstream environments.
Solution
Predictive Maintenance with AI Insights
We integrate live sensor data with historical performance to detect anomalies, predict failures, and optimize maintenance schedules. This minimizes unplanned downtime and significantly extends equipment life.

Complex Operations with Disconnected Systems
Disparate platforms (e.g., SCADA, ERP, CMMS) create silos that delay response and reduce efficiency.
Solution
Integrated Digital Operations Platform
Our Digital Twin connects all systems into one actionable interface. Operators, engineers, and managers gain a holistic view for better collaboration, faster decisions, and reduced operational friction.

High-Risk Environments and Safety Concerns
Oil & gas sites involve hazardous conditions, regulatory compliance needs, and workforce safety challenges.
Solution
Remote Monitoring & Virtual Inspections
The Digital Twin enables remote inspections, real-time risk assessments, and virtual walkthroughs. Workers can avoid unnecessary site visits and ensure compliance through visual evidence and audit trails, enhancing overall safety.

Inaccurate Asset Records and Inefficient Planning
Outdated 2D drawings or missing data make shutdown planning, retrofits, and upgrades risky and inefficient.
Solution
Accurate, Continuously Updated Asset Models
We provide 3D models enriched with comprehensive metadata, operational context, and change tracking. This ensures accurate planning, safer execution, and better handover between engineering and operations.
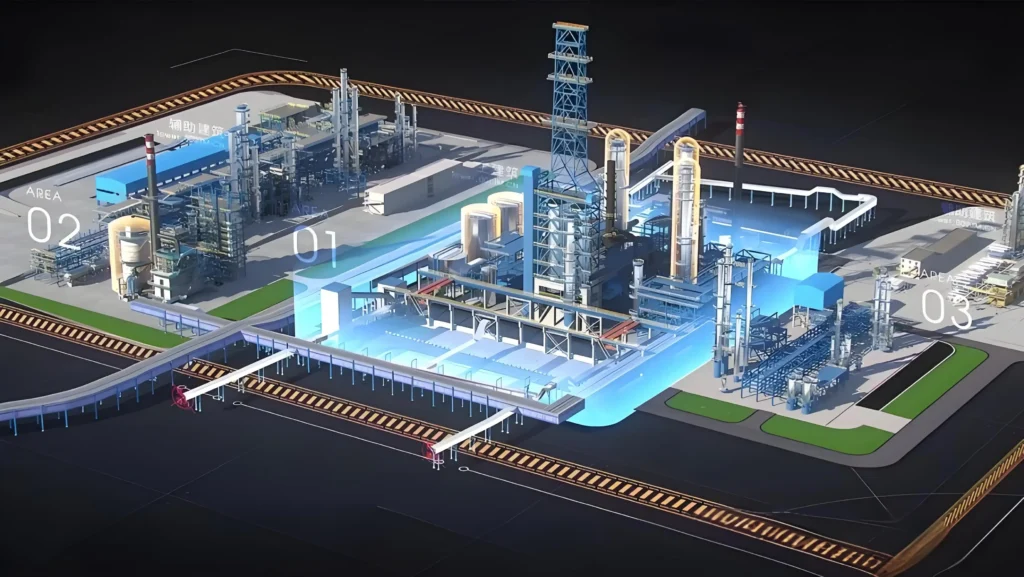
Results You Can Expect
✅Reduce downtime
✅ Lower maintenance costs
✅ Improve asset utilization
✅ Enhance safety and compliance
✅ Enable remote collaboration and smarter decisions
Apply It Across the Value Chain
Our Digital Twin platform is designed for upstream, midstream, and downstream segments:
- Offshore platforms & FPSOs
- Pipeline infrastructure
- LNG & gas processing facilities
- Refineries & petrochemical plants
- Storage terminals & distribution centers.
Let us show you how a Digital Twin can transform your operations.
to explore a custom solution for your oil & gas environment.