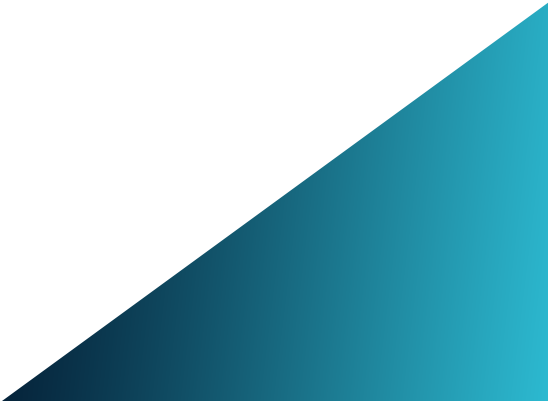
Transform Your Factory with Digital Twin Technology
Welcome to the future of manufacturing. Our Digital Twin Factory Solution empowers businesses to achieve seamless integration, real-time monitoring, and data-driven decision-making. We provide a virtual replica of your factory that enables precise monitoring, optimization, and control. Say goodbye to inefficiencies, bottlenecks, and costly downtime—embrace a fully connected, data-driven manufacturing environment.
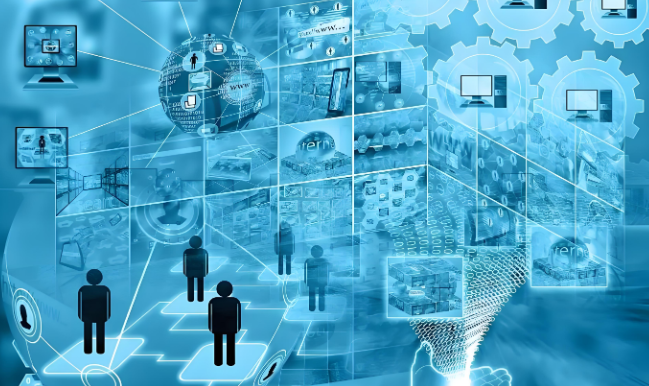
Revolutionizing Factory Management with Digital Twin Technology

Monitor and analyze production processes with real-time data insights

Optimize workflows to enhance productivity and efficiency

Minimize operational costs through predictive maintenance and automation

Enhance product quality by identifying and mitigating defects early

Improve decision-making with AI-powered analytics and simulations

Ensure seamless integration across production, supply chain, and energy management
With our solutions, you gain full visibility, control, and optimization across your entire factory—driving efficiency, reducing waste, and boosting profitability.
Challenges in Traditional Factory Operations
Modern manufacturing faces significant challenges that hinder efficiency and competitiveness:
- Siloed Data: Production data is fragmented across multiple systems, leading to inefficiencies in execution and monitoring.
- Unpredictable Production Delays: Urgent orders, equipment failures, and process changes make real-time production planning difficult.
- Lack of Real-Time Site Visibility: Complex production cycles and frequent deliveries make tracking production progress and managing resources a challenge.
- Inefficient Equipment Management: Unstructured maintenance processes and lack of predictive monitoring lead to unexpected failures.
- Limited Data Utilization: Factories struggle to collect, analyze, and leverage operational data for continuous improvement.
Our Digital Twin solution eliminates these inefficiencies by offering a centralized, intelligent platform for complete factory management and optimization.
Our Solutions
How We Transform Your Factory
Our digital twin solution addresses these challenges head-on, delivering measurable results:

Increased Management Efficiency (20-30%)
- Unified data integration eliminates silos, enabling faster decision-making
- Automated insights improve production planning and resource allocation

Boost Production Efficiency (10-30%)
- Centralize data on processes, plans, quality, and logistics.
- Compare real-time data with historical trends to optimize workflows and reduce bottlenecks

Reduced Labor Costs (10-20%)
- Automated data collection and visualization eliminate manual tracking
- Predictive maintenance reduces manual inspections and downtime

Lower Equipment Failure Rate (10-20%)
- Monitor equipment health in real time, diagnose faults, and predict potential issues.
- AI-powered fault diagnostics and predictive maintenance enhance reliability
- Implement preventive maintenance to reduce downtime and extend equipment lifespan.
“Digital twins are not simply "virtual reality", they are data-driven productivity optimization, with simulation and optimization at its core”
Core Features of Our Digital Twin Solution
Our solution integrates every stage of production into a single intelligent ecosystem:
- People Management: Real-time tracking of workforce activities and efficiency.
- Equipment Monitoring: Monitor equipment performance, locate alarms accurately, and provide maintenance teams with actionable insights.
- Material Tracking: Integrate with WMS and MES platforms to track inventory and production line materials in real time.
- Process Optimization: Standardize operating instructions and monitor process parameters to ensure consistent quality.
- Environmental Compliance: Live monitoring of emissions, waste, and sustainability metrics.
- Quality Control: Defect detection, root-cause analysis, and automated compliance reporting.
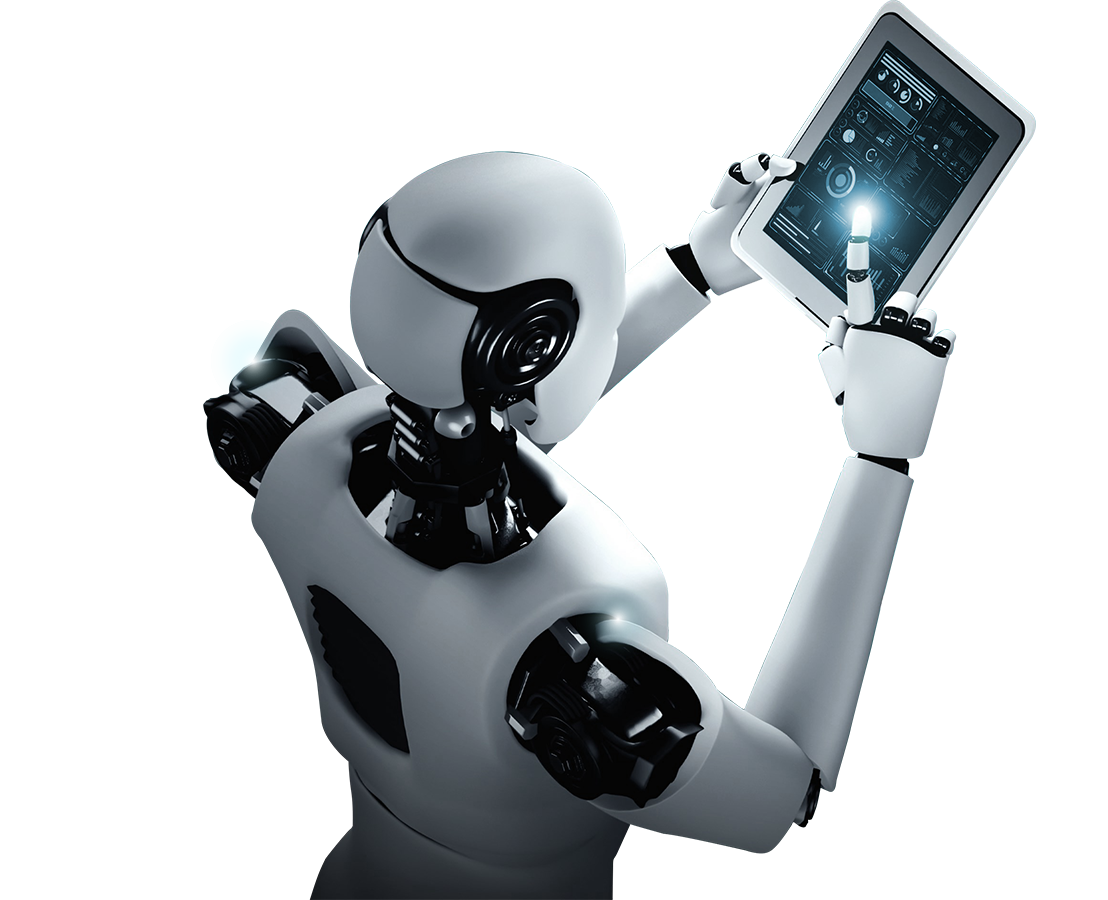
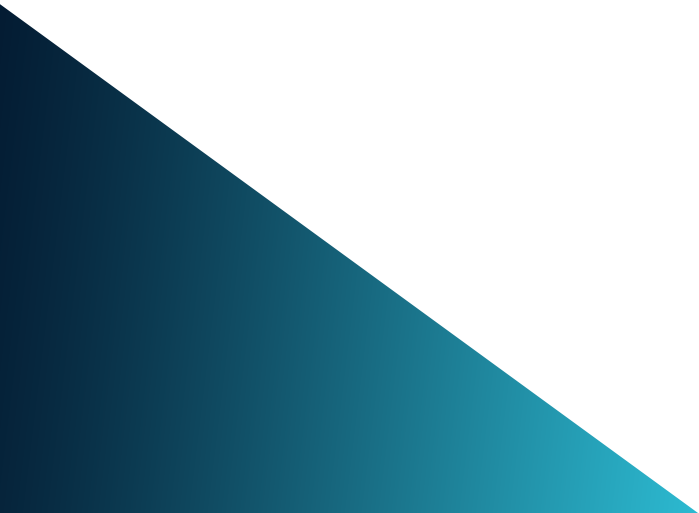
Factory Energy Management for Sustainability
In today’s energy-conscious world, our Energy Management System (EMS) helps you reduce costs and meet sustainability targets:
- Real-Time Energy Monitoring: Track energy consumption, supply, and environmental factors like temperature and humidity.
- Early Warning Systems: Detect anomalies and optimize energy usage to minimize waste.
- Carbon Management: Calculate carbon footprints, manage emissions, and implement effective reduction strategies.
Results You Can Expect:
- 20% Improvement in energy consumption measurement accuracy.
- 15% Reduction in energy costs through optimized usage.
- 10% Savings in labor management costs via automated data collection.
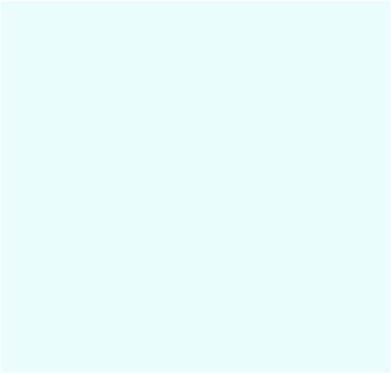
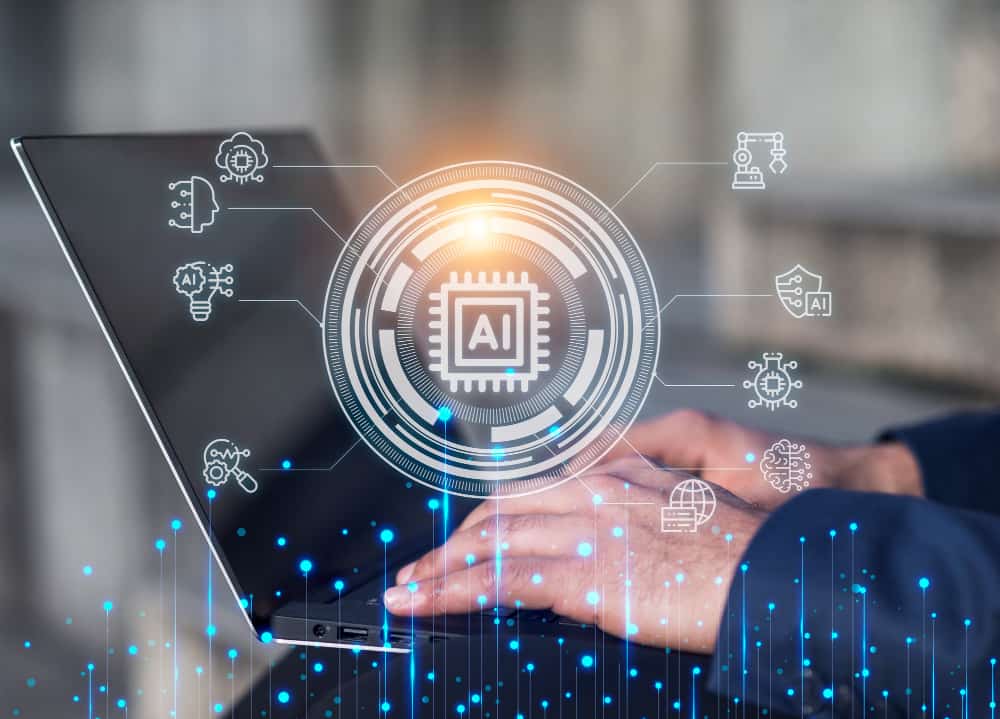
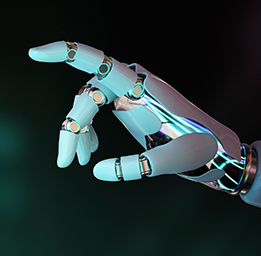
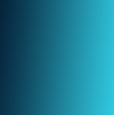
Remote Equipment Diagnosis & Predictive Maintenance
Traditional maintenance is reactive and costly. Our Remote Diagnosis System uses AI, IoT, and cloud computing to:

Predict potential failures and minimize downtime

Enable AR-based remote troubleshooting for real-time repairs

Increase equipment efficiency by 20% and reduce failures by up to 90%
Empower Your Factory with Digital Operations
In the age of Industry 4.0, digital transformation is no longer optional. Our comprehensive digital operations platform integrates:

Intelligent content and marketing solutions for brand positioning

Customer relationship management (CRM) for enhanced sales and support

AI-powered data analytics to optimize business growth
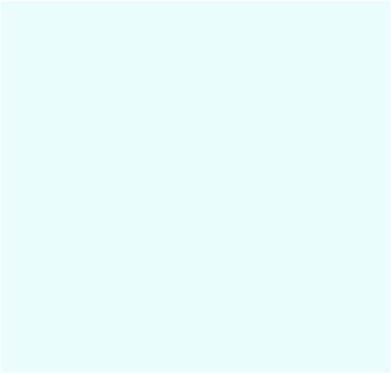
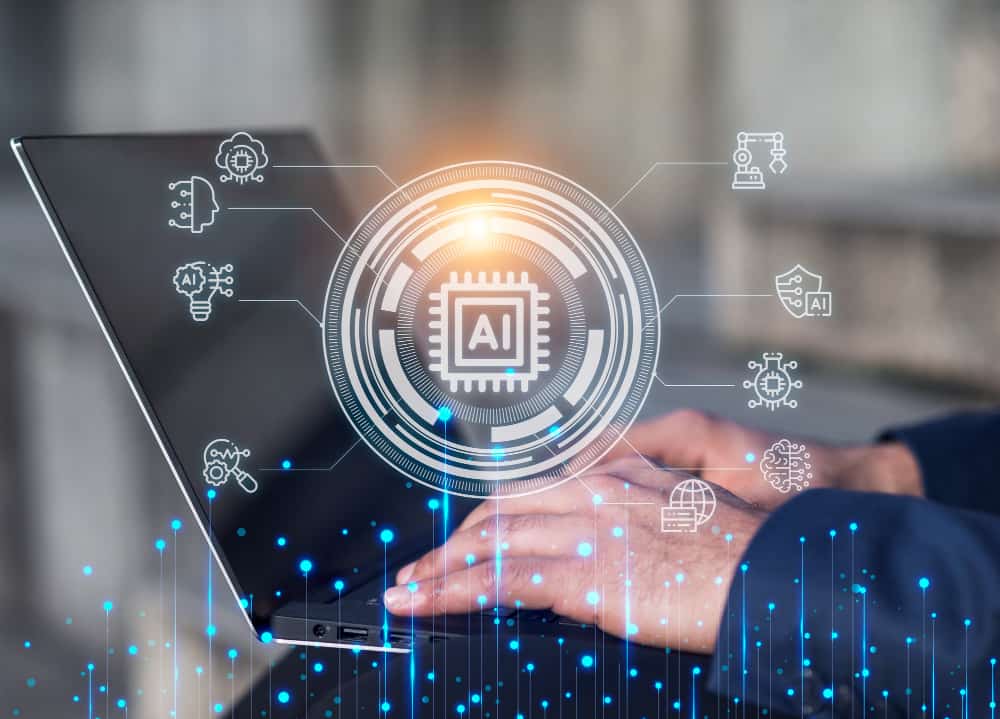
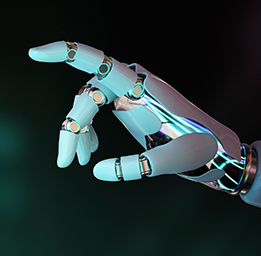
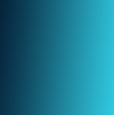
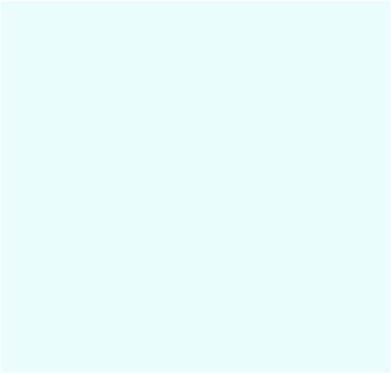
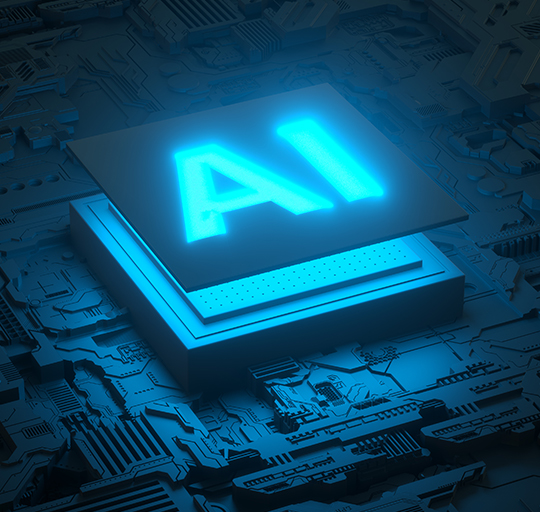
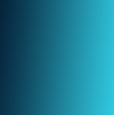
Why Choose Us?
- Cutting-Edge Digital Twin Technology to transform your factory operations
- Custom-Tailored Solutions to meet your unique manufacturing needs
- Seamless Integration with your existing systems and processes
- Proven Expertise in industrial digital transformation
- Scalable & Future-Ready to evolve with your factory's growth
Get Started Today!
Ready to transform your factory into a fully optimized, data-driven powerhouse? Contact us today to learn more about how our Digital Twin solutions can revolutionize your production processes, enhance efficiency, and drive profitability.